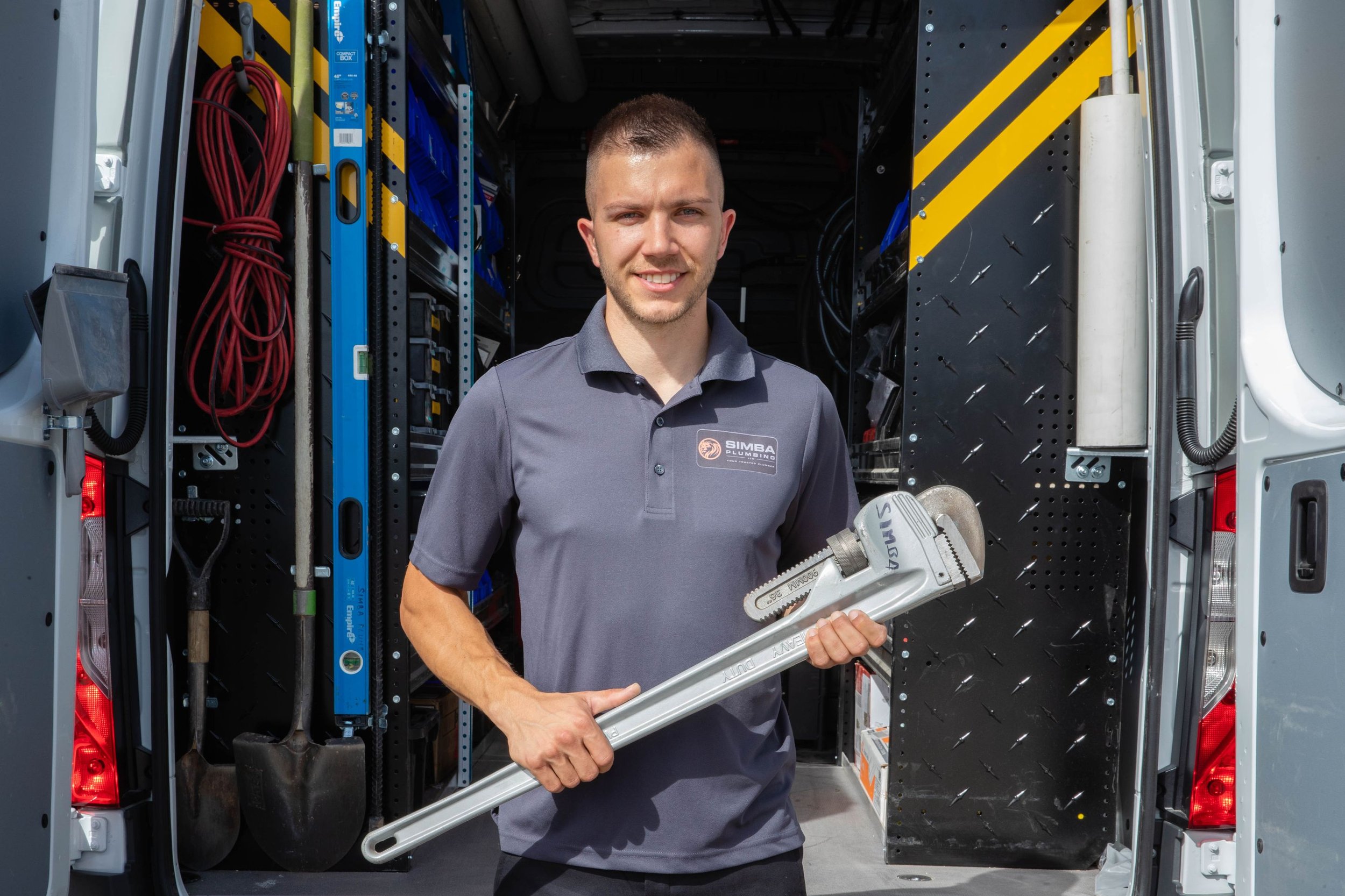
Backflow Prevention Installation in Phoenix, AZ
Backflow prevention installation in Phoenix is critical in maintaining a clean and safe water supply. By installing backflow prevention devices, contaminated water is effectively kept from entering the main water supply, thereby protecting the health of residents and businesses. Proper installation of these devices supports regulatory compliance and contributes to a safer community environment.
Backflow prevention systems are designed to stop the reverse flow of potentially contaminated water into clean water sources; for properties with irrigation systems, swimming pools, or other features connected to the main water line, backflow prevention devices act as essential barriers against contamination. A qualified technician installs and tests these systems to meet local standards, ensuring they operate effectively.
Regular maintenance and inspections are recommended for backflow prevention devices to keep them functioning at peak performance. Phoenix’s climate and water conditions can put extra pressure on these systems, making periodic checks essential for optimal operation. With reliable backflow prevention, residential and commercial properties contribute to a cleaner water supply, ultimately supporting public health and safety throughout Phoenix.
The Importance of Backflow Prevention in Phoenix
-
Protection Against Contaminated Water
Backflow prevention devices are critical barriers against water contamination in Phoenix's plumbing systems. These devices block contaminated water from flowing backward into clean water supplies, maintaining the integrity of drinking water. During pressure changes or system disruptions, contaminated water can enter the main water supply, creating health hazards. Professional installation and maintenance of backflow prevention devices safeguard the water supply against pollutants, chemicals, and other harmful substances.
-
Compliance with Regulations
Phoenix municipal codes mandate functional backflow prevention systems for commercial and residential properties. Property owners must schedule annual testing with certified professionals and maintain detailed inspection records. Meeting these requirements prevents costly penalties and potential liability issues. The local water authority conducts periodic audits to verify compliance with safety standards. Regular maintenance and testing documentation demonstrate adherence to municipal regulations while protecting community water supplies.
-
Prevention of Financial Losses
Effective backflow prevention shields property owners from substantial financial burdens associated with water contamination incidents. Beyond immediate repair costs, contamination events can lead to business interruptions, property damage, and potential legal liabilities. Installing and maintaining proper backflow prevention systems represents a fraction of potential cleanup and remediation expenses. Investing in quality equipment and regular maintenance protects valuable assets and prevents costly water quality emergencies.
-
Maintaining Water Quality
Backflow prevention systems preserve water quality throughout Phoenix properties. These devices maintain proper pressure differentials and prevent cross-contamination between potable and non-potable water sources. Regular maintenance keeps the mechanisms functioning optimally, blocking potential contaminants from entering the water supply. Professional testing identifies potential issues before they compromise water quality, maintaining safe and clean water throughout the property.
-
Protecting Equipment and Plumbing Systems
Backflow prevention devices shield valuable plumbing infrastructure from damage caused by pressure fluctuations and contaminated water. These systems prevent corrosive substances from entering pipes and fixtures, extending their operational lifespan. Regular maintenance of backflow preventers protects connected appliances and equipment from harmful substances. This protection preserves the integrity of building systems while maintaining proper water pressure throughout the property.
-
Peace of Mind for Property Owners
Professional backflow prevention installation creates a reliable barrier against water contamination risks. Regular testing and maintenance by certified professionals validate system performance and identify potential issues early. Documentation of proper backflow prevention demonstrates responsible property management and commitment to safety. This proactive approach to water system protection reduces stress about potential contamination incidents and regulatory compliance.
Signs a Property May Need a New Backflow Prevention Device in Phoenix
-
Water seepage around valve connections or continuous dripping indicates deteriorating backflow prevention components. Mineral deposits and discoloration near the device suggest ongoing leakage issues. These symptoms often signal internal valve failures or worn seals requiring immediate attention. A professional inspection can determine whether repairs or complete replacement will resolve the leakage and restore proper system function.
-
Test: When backflow prevention devices fail mandatory testing, replacement becomes necessary to maintain regulatory compliance. Test failures indicate compromised internal components that cannot reliably prevent contamination. Professional evaluation determines whether repairs can restore functionality or if complete replacement offers the most cost-effective solution. Swift action following test failures maintains proper system protection and regulatory compliance.
-
Fluctuating water pressure or persistent low-pressure conditions may indicate failing backflow prevention devices. Pressure irregularities can stem from worn internal components or improper valve function. These symptoms often appear gradually as device components deteriorate. A professional diagnosis can identify whether backflow prevention problems cause pressure issues and recommend appropriate solutions.
-
Changes in water quality, including unexpected tastes or odors, may indicate backflow prevention failure. These symptoms suggest possible cross-contamination between potable and non-potable water sources. Immediate professional inspection can identify whether compromised backflow prevention allows contamination. Swift investigation of water quality changes protects building occupants and identifies necessary system repairs.
-
Backflow prevention devices typically require replacement after 10-15 years of service, depending on water conditions and usage patterns. Component deterioration accelerates in areas with hard water or high mineral content. Environmental factors and frequency of use impact device longevity—regular professional inspections track device age and condition to plan appropriate replacement timing.
-
Multiple repair incidents within short periods indicate declining device reliability. Recurring problems suggest systemic deterioration rather than isolated component failures. The cumulative cost of frequent repairs often exceeds replacement expenses. A professional evaluation can determine whether complete device replacement offers more cost-effective long-term protection than continued repairs.
OUR REVIEWS
Our goal is to provide the best service and customer experience.
Types of Backflow Prevention Devices We Install in Phoenix
-
RPZ assemblies provide maximum protection against backflow in high-hazard applications. These sophisticated devices contain multiple check valves and a pressure-differential relief valve system. The design creates isolated pressure zones, preventing contamination even under extreme conditions. RPZ assemblies protect water supplies near chemical processing, medical facilities, and industrial operations. Regular testing validates the relief valve's ability to discharge water when pressure differentials fall below acceptable levels.
-
Double-check valve assemblies offer reliable protection for moderate hazard applications. These devices incorporate two independent check valves working in sequence to prevent backflow. The robust design withstands varying pressure conditions while maintaining consistent protection. These assemblies work effectively in commercial buildings, apartment complexes, and irrigation systems. Regular maintenance keeps both check valves operating at peak efficiency throughout their service life.
-
Pressure vacuum breakers provide specialized protection for irrigation and similar outdoor applications. The internal air inlet valve closes under typical flow conditions and opens when pressure drops occur. This design prevents back-siphonage while allowing normal water flow. PVBs require installation above all downstream piping and outlets. These devices maintain reliable protection in varying weather conditions and seasonal usage patterns.
-
Atmospheric vacuum breakers offer essential backflow protection through a simple yet effective design. The floating disc mechanism responds to pressure changes, preventing back-siphonage in low-hazard applications. AVBs function well in residential irrigation systems and simple commercial applications. The straightforward design requires minimal maintenance while providing consistent protection. Installation must remain above all downstream piping for proper operation.
Our Backflow Prevention Installation Process in Phoenix
-
Initial Site Assessment and Inspection
Comprehensive site evaluation begins with analyzing existing plumbing systems and identifying potential cross-connections. Professional inspectors examine the property's water usage patterns, pressure conditions, and contamination risks. This detailed assessment reveals specific protection requirements and installation constraints. The inspection includes documenting current system conditions and identifying necessary upgrades to meet safety standards.
-
Device Selection
Professional analysis determines the most appropriate backflow prevention device based on specific site conditions. Hazard level, installation location, and water usage patterns guide device selection. The selection process considers local code requirements and industry best practices. Proper device selection balances protection requirements with operational efficiency and maintenance considerations.
-
Preparation for Installation
Thorough preparation involves coordinating water service interruptions and gathering necessary materials and equipment. The installation team reviews site-specific safety requirements and establishes appropriate work zones. Preparation includes protecting surrounding property and verifying compatibility with existing plumbing systems. Advanced planning minimizes disruption while maintaining proper safety protocols throughout the installation process.
-
Installation of the Device
Professional technicians follow manufacturer specifications and industry standards during device installation. Proper positioning and secure mounting prevent stress on connecting pipes and fittings. The installation process includes adding appropriate support structures and protection from environmental factors. Careful attention to installation details promotes long-term reliability and simplified maintenance access.
-
Initial Device Testing
Comprehensive testing validates proper installation and operation under various pressure conditions. Technicians measure pressure differentials and verify relief valve function in RPZ assemblies. Testing procedures follow manufacturer specifications and local regulatory requirements. Documentation of initial test results establishes baseline performance data for future reference.
-
Certification and Compliance
Professional certification involves thorough documentation of device specifications and installation details. Required forms and test results are submitted to local authorities for validation. The certification process includes recording serial numbers and installation dates for future reference. Complete documentation demonstrates full compliance with municipal regulations and industry standards.
-
Post-Installation Review
A detailed system evaluation confirms proper device operation and integration with existing plumbing systems. The review process includes checking for leaks and verifying proper pressure readings throughout the system. Documentation of final settings and operational parameters provides a reference for future maintenance. This systematic review validates complete system functionality.
-
Cleanup and Final Walkthrough
Following installation completion, professional crews restore the work area to its original condition. The cleanup process includes removing all installation materials and verifying site safety. A final inspection confirms proper device labeling and accessibility for future maintenance. The walkthrough process documents completed work and addresses any remaining questions about system operation.
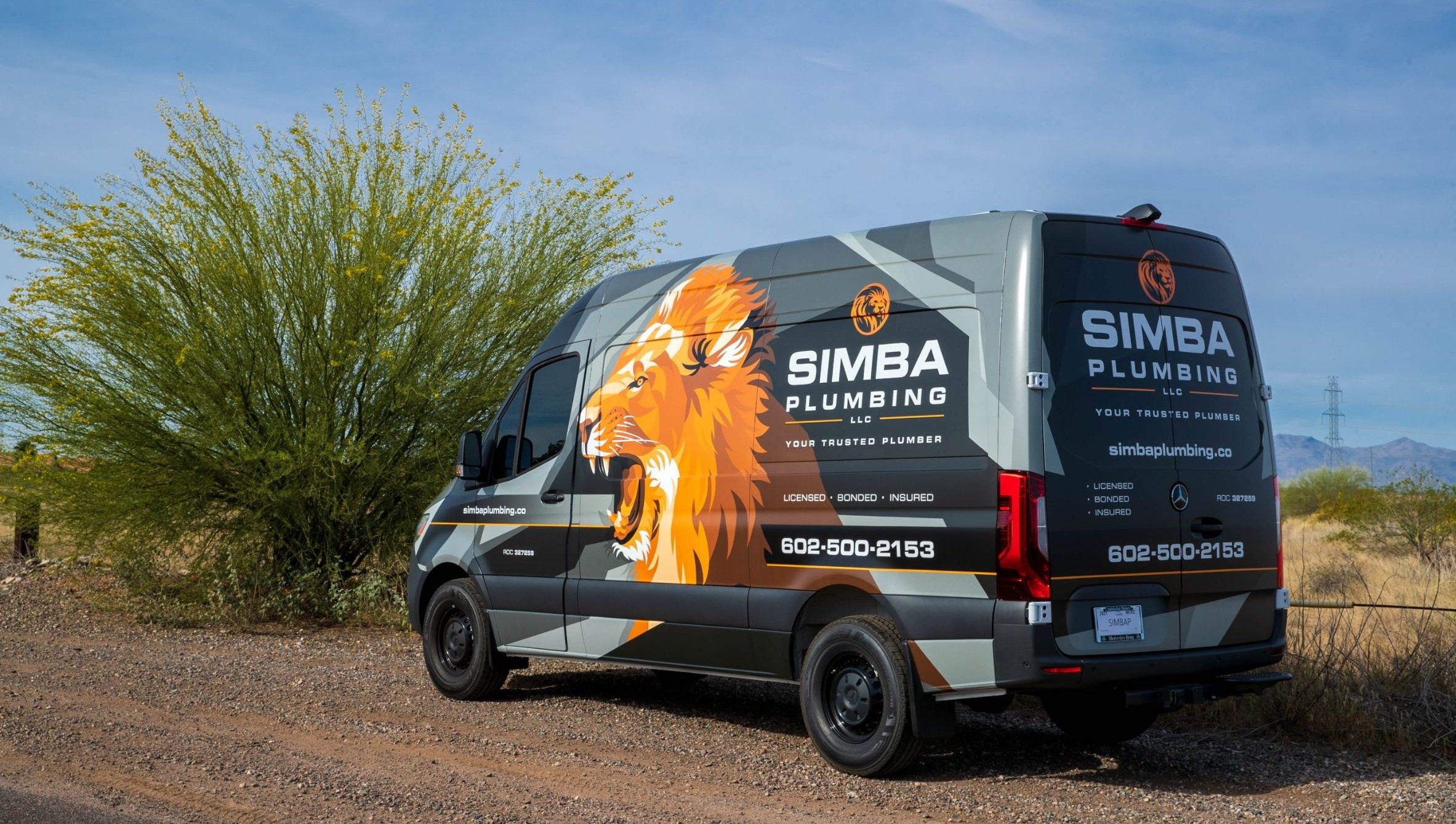
Areas we serve
Phoenix, Sun City West, Mesa, Chandler, Gilbert, Glendale, Scottsdale, Peoria, Tempe, Surprise, Goodyear, Avondale, Queen Creek, El Mirage, Fountain Hills, Paradise Valley, Tolleson, Youngtown, Litchfield Park, Cave Creek, Carefree, Sun Lakes, and Waddell
Why Choose Simba Plumbing LLC for Backflow Prevention Installation in Phoenix
-
Simba Plumbing LLC brings extensive backflow prevention system design and installation knowledge. The company's track record spans numerous successful installations across diverse commercial and residential properties. Their experienced team understands local water conditions and specific protection requirements. This specialized expertise translates into effective solutions for complex installation challenges.
-
Each Simba Plumbing technician is certified in backflow prevention installation and testing. The team maintains comprehensive knowledge of evolving industry standards and local regulations. Regular professional development keeps skills current with new technologies and installation methods. This dedication to certification demonstrates a commitment to installation quality and safety standards.
-
Simba Plumbing maintains detailed knowledge of Phoenix municipal codes and state regulations regarding backflow prevention. The company follows strict protocols for installation documentation and compliance reporting. Their systematic approach meets all regulatory requirements for device selection and installation. Professional relationships with local authorities facilitate smooth permit processing and inspections.
-
Professional scheduling and project management keep installations on track and minimize disruptions. The company maintains an adequate inventory of approved devices for prompt installation. Efficient work processes reduce system downtime while maintaining installation quality. Clear communication throughout the process informs property owners of progress and completion timelines.
For reliable Backflow Prevention Installation in Phoenix, AZ, contact Simba Plumbing LLC.
FAQs
-
Backflow prevention is a system installed to protect your clean water supply from contamination due to reverse flow. It’s crucial to ensure that hazardous substances do not enter your water supply, keeping your home and community safe.
-
A backflow prevention system should be installed when required by local building codes, especially if your property has irrigation systems, fire suppression systems, or other connections to non-potable water sources.
-
Yes, local water authorities often require backflow prevention systems to ensure the safety of public water supplies in Phoenix. Check your local regulations to determine if you need one.
-
Typical types include the Reduced Pressure Zone (RPZ) valve, Double Check Valve (DCV), and Pressure Vacuum Breaker (PVB). The appropriate choice depends on your system and the level of protection required.
-
You likely need a backflow prevention device if you have an irrigation system, pool, fire sprinkler system, or any other connection that could potentially contaminate the potable water supply.
-
The installation process usually takes a few hours, depending on the complexity of the system and any necessary permits. Our experienced plumbers at Simba Plumbing will ensure a fast, efficient installation.
-
It is recommended that a licensed plumber install your backflow prevention system. This ensures that the installation is up to code and provides the necessary protection for your home.
-
Yes, most backflow prevention installations require a permit. Simba Plumbing will handle the permitting process for you to ensure compliance with local regulations.
-
Backflow prevention devices should be tested every year to ensure they are functioning correctly. Simba Plumbing can provide this testing service to keep your system in shape.
-
Failing to install a backflow prevention system when required can result in contamination of the public water supply, potential fines, and health risks to your family and neighbors.
-
The cost varies depending on the device type and the installation's complexity. Simba Plumbing offers competitive pricing and will provide a free estimate before work begins.
-
Routine maintenance includes testing, inspections, and occasional cleaning. Our team at Simba Plumbing offers maintenance services to keep your backflow prevention system working correctly.
-
If you suspect a problem with your backflow device, contact Simba Plumbing immediately. Our team can identify and fix the issue to guarantee your system functions correctly.
-
In some cases, backflow prevention devices can be repaired. If a repair is not possible, we will recommend a replacement. Simba Plumbing can advise you on the best course of action for your specific situation.
-
Yes, Simba Plumbing provides backflow prevention installation services for residential and commercial properties in Phoenix. Our team can assess your business’s needs and recommend the best solution.